La determinación del intervalo apropiado para el reemplazo de los cojinetes del compresor de tornillo implica una combinación de factores, que incluyen las condiciones de operación, el historial de mantenimiento y el monitoreo del desempeño. He aquí un enfoque sistemático:
Condiciones de funcionamiento: El entorno operativo de un compresor de tornillo puede variar ampliamente dependiendo de factores como la industria, la aplicación, la ubicación geográfica y las condiciones ambientales. Los compresores utilizados en plataformas marinas de petróleo y gas enfrentan desafíos diferentes en comparación con los que operan en instalaciones industriales o plantas de fabricación. El análisis de los matices de las condiciones operativas permite al personal de mantenimiento identificar posibles factores estresantes que pueden acelerar el desgaste de los rodamientos, como la exposición a gases corrosivos, altos niveles de humedad o arranques y paradas frecuentes. Al cuantificar estos factores y su impacto en el rendimiento de los rodamientos, los usuarios pueden adaptar su enfoque de mantenimiento para abordar desafíos específicos de manera efectiva.
Historial de mantenimiento: una revisión exhaustiva del historial de mantenimiento proporciona información valiosa sobre las tendencias de rendimiento de los rodamientos de compresores de tornillo a lo largo del tiempo. Permite a los usuarios identificar patrones de fallas, problemas recurrentes o desviaciones inesperadas de las métricas de desempeño esperadas. El análisis de datos históricos permite a los equipos de mantenimiento correlacionar las actividades de mantenimiento con la confiabilidad y el tiempo de actividad del equipo, identificando áreas de mejora y optimización. Al aprovechar los registros históricos de mantenimiento, los usuarios pueden desarrollar estrategias proactivas para mitigar riesgos conocidos, mejorar las prácticas de mantenimiento y extender la vida útil de componentes críticos como los rodamientos.
Monitoreo del desempeño: el monitoreo del desempeño no se limita a evaluaciones periódicas, sino que abarca el monitoreo continuo en tiempo real de parámetros operativos clave. Por ejemplo, los sistemas modernos de compresores de tornillo están equipados con sensores y dispositivos de monitoreo que proporcionan una gran cantidad de datos sobre variables como niveles de vibración, gradientes de temperatura, fluctuaciones de presión y consumo de energía. Al aprovechar las tecnologías de monitoreo avanzadas y las herramientas de análisis de datos, los usuarios pueden detectar cambios sutiles en el comportamiento de los rodamientos que pueden indicar una falla inminente. El monitoreo del desempeño en tiempo real permite la toma de decisiones proactiva, lo que permite a los equipos de mantenimiento intervenir antes de que los problemas aumenten y afecten la producción.
Monitoreo de condición: el monitoreo de condición va más allá de los enfoques de mantenimiento tradicionales al centrarse en la detección temprana de condiciones operativas anormales y modos de falla incipientes. Implica implementar un conjunto de técnicas de diagnóstico, que incluyen análisis de vibraciones, análisis de aceite, termografía, pruebas ultrasónicas y monitoreo de emisiones acústicas. Estas técnicas permiten al personal de mantenimiento evaluar el estado de los rodamientos de los compresores de tornillo de forma no invasiva e identificar problemas potenciales antes de que se manifiesten como fallas catastróficas. Al integrar el monitoreo de condición en las prácticas de mantenimiento de rutina, los usuarios pueden minimizar el tiempo de inactividad no planificado, optimizar los programas de mantenimiento y maximizar la confiabilidad del equipo.
Evaluación de riesgos: La evaluación de riesgos es un proceso sistemático para evaluar la probabilidad y las consecuencias de posibles escenarios de falla asociados con los rodamientos de compresores de tornillo. Implica identificar peligros, evaluar riesgos, priorizar medidas de mitigación y desarrollar planes de contingencia. Durante el proceso de evaluación de riesgos se tienen en cuenta factores como la criticidad del equipo, el impacto de las fallas en los procesos de producción, los requisitos de cumplimiento normativo y las consideraciones de seguridad. Al cuantificar los riesgos y sus posibles consecuencias, los usuarios pueden asignar recursos de manera efectiva, priorizar las actividades de mantenimiento e implementar intervenciones específicas para reducir la probabilidad de fallas relacionadas con los rodamientos.
Screw Compressor Rodamientos axiales de rodillos esféricos
Screw Compressor Rodamientos axiales de rodillos esféricos
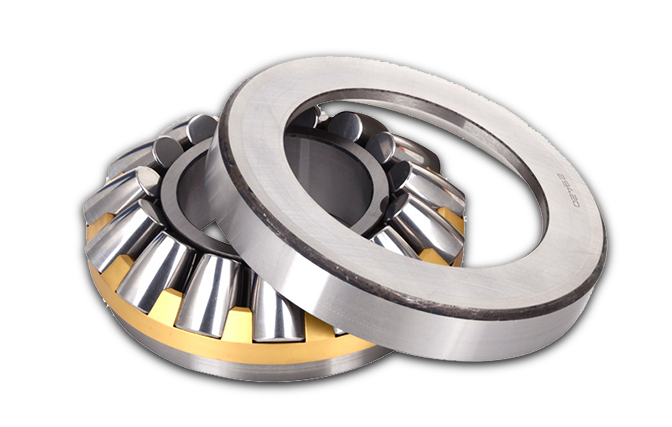
Los rodamientos axiales de rodillos autoalineantes DHK están disponibles en tres configuraciones diferentes basadas en diferentes dimensiones y diseños de jaula.
Los rodamientos de rodillos autoalineantes de tamaño pequeño y mediano pueden ser de jaula de cobre macizo (sufijo MB) o de acero estampado (sufijo J);
La estructura estándar para los rodamientos de rodillos autoalineantes de gran tamaño es una jaula de cobre macizo (sufijo MB).